Thermal capacities
proven thermal performance
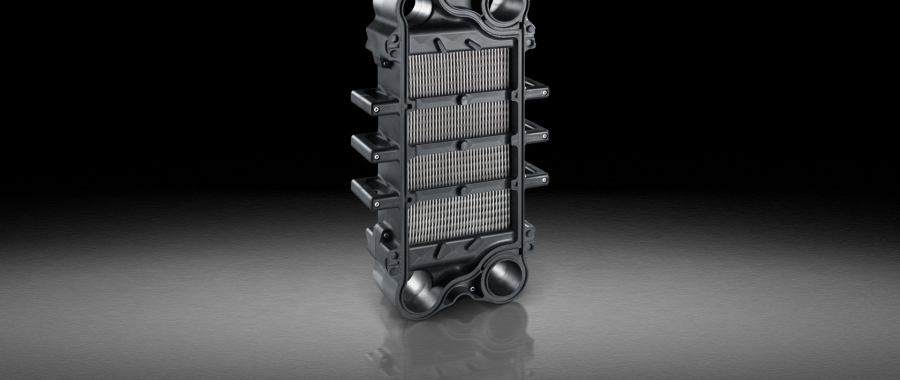
Creating a new type of heat exchanger, it has been important for us not to compromise on the thermal capabilities of the highly developed plate heat exchanger. Consisting of 0,5mm titanium, pleated to approximately 3,2mm pocket widths, the Pleat heat exchanger elements offer an area-to-volume ratio of ca 270 m2/m3. The height of the titanium walls is 60mm for all sizes.
But can the heat transfer values also match those of a plate heat exchanger? The Pleat heat exchanger has been tested in the new Sperre lab, and the results were indeed interesting. The picture below shows testing of early prototype.
For comparison, the Pleat DN65 heat exchanger was tested together with a "top brand" gasketed heat exchanger (also DN65, 2.2m2 heat transfer area). Dark red lines show the measured K-values, green lines show pressure drop for sea water, while blue lines show pressure drop for fresh water. Continuous lines for Pleat, dotted lines for PHE.
It must be emphasized that it is difficult to find the exact values for the hydraulic diameter and the available flow area for the PHE, and these values will also decrease somewhat as the PHE is torqued up. It might also be a matter of definition/discussion how much of the top & bottom distribution area should be considered as heat transfer area.
Our conclusion of this test is that the thermal performance (K-value) of the Pleat heat exchanger can be approximated to that of a PHE. The curves for pressure drop are however significant lower, indicating that nearly the same heat transfer comes at a much lower cost (pump work).
Thermal calculations
At the Hydroniq lab, measurements are gathered for numerous combinations of flows, number of passes and elements. The results are thoroughly analyzed, and the outcome is a theoretical heat transfer based on the nusselt number:
The heat transfer numbers for each liquid and the titanium wall give the total heat transfer when arranged together in the well known fraction sum:
These equations are the basis for calculating adequate cooling, based on the customer's input. The way ahead is in most cases based on the Ɛ-NTU-method, as some temperatures in most cases are unknown.
Corrugation pattern
The corrugation pattern chosen is the so-called Chevron (or Herringbone) pattern. This pattern has two important features:
It can be pressed similarly on all walls, and after pleating, the neighboring walls possess opposite (crossing) patterns that withstand differential pressure.
Being arranged in a certain way, the Chevron pattern shows favourable behavior regarding dirt removal when cleaned with a water jet washer.