Pleat Cooler VS
Plate Heat Exchangers (PHE)
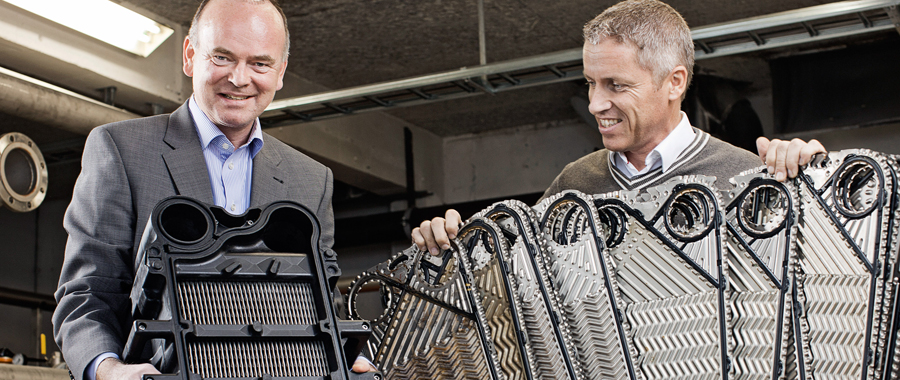
The patented Pleat cooler combines the best from two worlds; performance as a traditional Plate Heat Exchanger, and maintenance-friendly as replacing an air filter. It consists of few, and handling-friendly elements. This allows any crew to gain better control in their systems, keeping the entire system cleaner and more efficient.
The Pleat Cooler can easily replace conventional gasketed Plate Heat Exchanger in the majority of installations, and also a minor part of the shell & tube market.
Equal functional issues
- K-value – the key parameter of efficiency is tested to be approximately equal to that of a PHE.
- Pressure drop – a sum of losses from inlet to outlet. Tests show strong results, with slightly lower pressure drop than PHE.
- Overall size – quite similar, but with shorter occupied length, due to fewer gaskets.
- Leakage control – both designed to avoid fluid mix in case of a gasket failure.
- Filter – both designed with capability for an inline filter.
- Process interface – both technologies have very similar interface, which allows for easy replacement for old to new technology.
Obvious differences
Less parts – the Pleat cooler has only 1 gasket, while an equal PHE has 15 gaskets for the same heat transfer area.
A typical sample – 4 elements vs 60 plates
For a typical mid-sized installation, a Pleat cooler will consist of the basic framework + 4 elements, with a total need for 5 rigid gaskets, whereas the same application with a Plate Heat Exchanger will consist of similar basic framework, require 60 individual plates and 61 gaskets. For the crew this is a totally different world when overhauling.
Competitive cost – less use of expensive material (titanium), and more use of more functional modern materials. This results in saved cost, and gains a lot of new valuable functionality.